I wasn't planning on writing the weekly blog this year. I had expected the run-up to Drag Week this year to be fairly sedate, with minimal changes to the car. When I put the car away for the winter last November it was running fine, with no issues. There were quite a few small updates that I wanted to do on the car, but I felt like if I had to I could have just changed the oil and gone off to another Drag Week.
The car situation seemed like a good thing, because from a family perspective 2016 has been a very tough year so far. My wife and my Dad were both beset by fairly serious illnesses and my mother-in-law passed away. Our neighbor down the street, whose family took care of our kids every day after school for several years while my wife and I were working, suddenly dropped dead of a heart attack; he was one day older than me. The dog got sick and nearly died, the cat was hit and killed by a car; this kind of stuff has just seemed to go on and on since the beginning of the year. On top of that my regular job has been a real challenge this year and has been causing me fits, and it has taken much longer than I expected to get my high riser and tunnel port intake adapter machining programs finished and working. Plus some of the new FE Power products have been delayed, notably the timing gear sets. I just haven’t had any time to think about Drag Week.
Finally, a couple of weeks ago after getting my tunnel port intake adapter CNC programs finished and working, I decided I’d better start working on the Shelby clone. I had a short list of updates I wanted to do, including finishing the work on the fiberglass bumpers so that they could be installed, installing a new EFI system with some updated wiring, and also putting some stops on the K-member that bolts under the car and holds the steering rack. You may recall from last year’s Drag Week blog that the steering rack is not securely mounted on the Fatman Fab K-member (one of the many issues I have had with this kit). I had problems during the event where the rack moved, and then the steering wheel angle changed and the car would pull to one side. During the event I resolved the problem by hammering on the steering rack to put it back in position. After Drag Week I was driving around my local area and had the same thing happen, so I wanted to drop the K-member and front suspension out of the car to try to fix this problem. I figured that welding some fabricated screw jacks on the K-member to contact the rack and hold it in place would solve the problem.
So, two weekends ago I dropped the K-member and front suspension out of the car. This left the bottom of the engine completely exposed, so I changed plans and decided to drop the pan and check the rod bearings. With a 4.6” stroke and running up to 7700 RPM, the rod bearings were always going to be a concern. I had been counting on the dry sump system to keep the bearings in good shape. I pulled the pan and the second pair of rods were straight down, so I pulled the #2 and #6 rod bearings first. They looked perfect, nearly unused! The coating was still on the complete bearing, no sign of it wearing off. I went ahead and replaced them anyway, but I probably could have just left them in there. I put the wrench on the front crank bolt and rotated it 90 degrees so that #1 and #5 were at the bottom. On #1 there was a scratch in the lower bearing shell, and there was a small area where the coating was nearly gone on the upper, but otherwise both sets of rod bearings looked beautiful. I replaced both sets.
Then, something very unexpected happened. As I rotated the crank another 90 degrees to get to the #3 and #7 rod bearings, I heard a big whoosh. What the heck was that? I looked towards the back of the car, and coolant was pouring out of the right side header tube! Oh no…
I got out from under the car and sat down to think for a while. The car had been sitting since November with coolant in it; I hadn’t drained it at the end of the year. It had been running fine up to that point. The garage is heated, and there was plenty of anti-freeze in the coolant, so it wasn’t possible that it had frozen. Based on the position of the pistons when I turned the crank the last time, I figured that the coolant had come from the #2 cylinder. Because of the spread bore spacing, I have to use custom copper head gaskets on this engine. After some consideration I figured that I’d probably had a minor head gasket leak, and coolant had been seeping into the #2 cylinder all winter. When I turned the crank, that cylinder must have been on the overlap stroke and all the coolant came out through the exhaust valve.
Well, this certainly shed a different light on the work I had ahead of me. If I was going to put head gaskets on the engine it was going to have to come out; I wasn’t going to disassemble and re-assemble the SOHC while it was in the car. But at least with the engine out and torn down I could get a really good look at the internal components to see how they fared over 2000+ miles of street driving and a bunch of trips down the race track.
I crawled back under the car to finish looking at the rod bearings. The #3, #4, and #7 bearings looked perfect, but I did find an issue with the rod bearings on #8. Both #8 bearing shells had lost their crush, indicating that they had gotten hot. Also, on the upper bearing there was a spot near the edge where the coating was worn away and the bearing material looked like it was cracked or flaking. See the photo of the #8 upper bearing shell below:
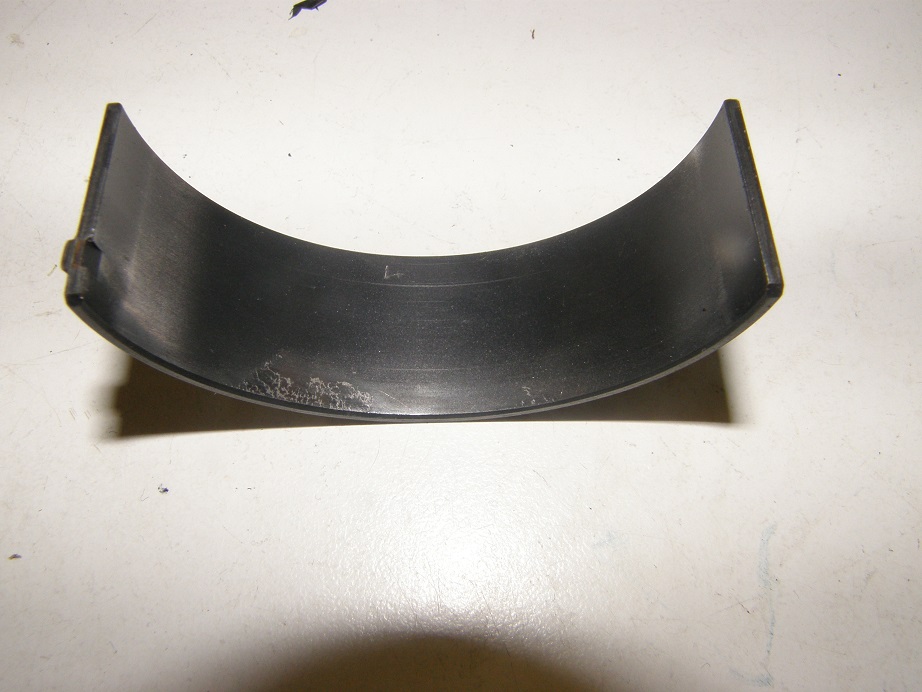
I’ve seen this before and this has been explained to me as evidence of extreme heat. Later that day I spoke with Blair P about this and he pointed out that the #8 rod gets its oil from the #5 main. He had me look up the clearances on the engine (I record these on a build sheet whenever I build an engine), and while main bearing clearances on the #1 through #4 mains were in the 0.0023” to 0.0027” range, clearance on #5 was 0.0032”. So that additional clearance on #5 may have contributed to this problem.
Later on that weekend while I was thinking about this some more, I realized with the engine out I could potentially address the issues in the #4 cylinder bore. Last summer when I damaged the engine on the dyno I had installed a new piston and rod in #4, put a quick hone on the cylinder, and run it. The hone had shown that there were two minor dings and a scratch in the cylinder bore. These were down about 1.5” from the top of the bore, and not very deep, so I had just run with them in there. But with the heads off the engine I could measure how deep those dings really were, and maybe hone the bore a little oversize and go to an oversize piston on that bore. So, maybe pulling the motor apart wasn’t such a bad thing if I could fix this minor issue.
Fast forward to last weekend. I had the engine mostly disconnected, and my friend and Drag Week co-pilot Steve (aka 57 Lima Bean and/or the Drunk Monkey) came over to help me get the engine out. We decided to leave the trans in the car and after some screwing around finally pulled the engine clear. Later that evening I started the tear down. As soon as I pulled the intake manifold I realized that the leak was not in the head gaskets, it was the head. The #2 intake port showed a clear coolant leak path:
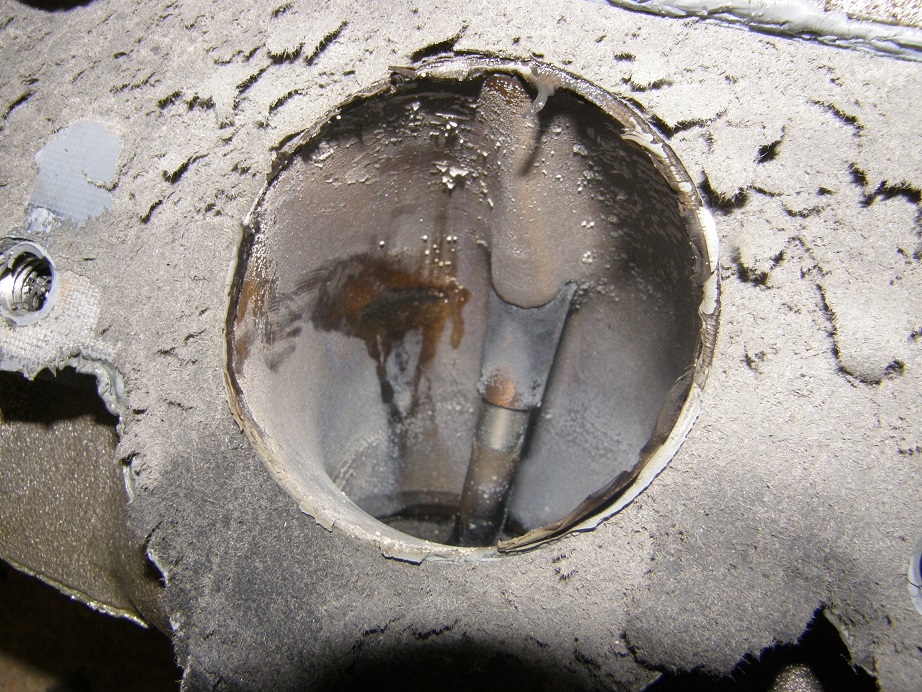
These heads had leaked when I got them; the castings showed a lot of porosity in the ports so I’d had them checked, and sure enough they leaked. But the leaks had been in the exhaust ports. When I took them in for a max effort porting job, my porting guy broke through into the water jacket in the intake ports, so all the intake ports had to be welded, in addition to the exhaust ports where the leaks had originally been found. Welding in the intake ports had been particularly troublesome, requiring several passes, so I assume that the welding in the #2 intake port was marginal and resulted in the coolant seepage I had discovered.
Now, with the addition of a cylinder head issue I had another decision to make. My original plan for DW16 was to run the existing set of heads. However I had been working on a new set of heads. I had dropped these heads off for porting at my porting guy’s place in November, and told him I needed them back at the end of January. These heads had never leaked, but I expected the same kind of issues with breaking through into the water jacket ports so I expected they would have to be welded also. As usual my porting guy took longer than originally planned but he did get an additional 30 cfm out of the heads, up to 475@0.800” on the intakes. Over the last couple of months I’ve been shuttling these heads from the porting guy to the welder and back, trying to get the welding done and sealed up so that eventually I could run the heads. After finding the leak in the existing heads, I decided I may as well run the new heads. The port configuration has changed though, so I will have to build a new intake manifold to work with these heads. I figured I could squeeze that in sometime in the next month, and still have the engine back together, on the dyno, and then back in the car by early August. Plenty of time (LOL!).
Back to the teardown. After getting the engine torn down to the short block, I rotated the crank so that I had a clear view of the two dings in the #4 cylinder wall, and went in there with my dial bore gauge to measure how deep they were. One was about 0.003” deep, and the other was about 0.005”. Increasing the bore past 0.009” in diameter wasn’t possible because of piston ring size constraints, so I ended up settling on a 0.008” overbore on that cylinder. That would take out the one ding and the scratch in the bore, and leave the other ding only about 0.001” deep and very narrow, probably less than 0.100” wide. I figured this would be an improvement and I could live with that. I had Blair order one piston for #4 at 0.008” oversize, for expedited one week delivery ($$$). Figured I’d have the piston the week of July 5, and could get the block honed to size and get the short block back together the weekend of July 9-10.
Last week I did my best to accelerate work on the new heads. They needed guides and seats, so I got those ordered and they should be delivered this coming week. My cylinder head guy has promised to get them finished up as soon as he gets the parts, and now that the heads have been welded and they passed the pressure check, I should have them by the weekend of July 16. Things were shaping up for the engine to be back together and on the dyno by the end of the month, and back in the car by early August.
Unfortunately, that whole plan may have gone out the window this weekend. Saturday morning I decided to tear down the short block. I needed to do that anyway so that the #4 cylinder could be honed for the new piston, but because of the connecting rod failure at DW14, I am now fully paranoid about connecting rods. So I decided to take the short block apart, pull the rods off the pistons, and get them magnafluxed just to be sure they were all still good. I pulled the first piston/rod assembly out of the block and started removing the rings. These pistons have the pin going through the oil ring groove, and use a support rail at the bottom of the oil ring groove to support the oil rings, so those rings have to come out in order to remove the pin. When I got to the oil rings, though, as I started to pull the top oil ring, I found that it was stuck in place part of the way around the piston. Hmmmm… I very carefully worked it loose, because I wanted to re-use these rings, since they were already seated to the bore. Then I removed the expander ring and the lower oil ring, and saw the problem. The oil ring support rail had moved!
There is a small dimple in the oil ring support rail that has to point down and line up with the pin hole. The dimple is supposed to keep the oil ring support rail from rotating past the pin hole. Obviously, this did not work, as the oil ring support rail had rotated over 90 degrees. When it rotated, the dimple on the bottom side dug a groove into the bottom oil ring land of the piston! See the photo below:
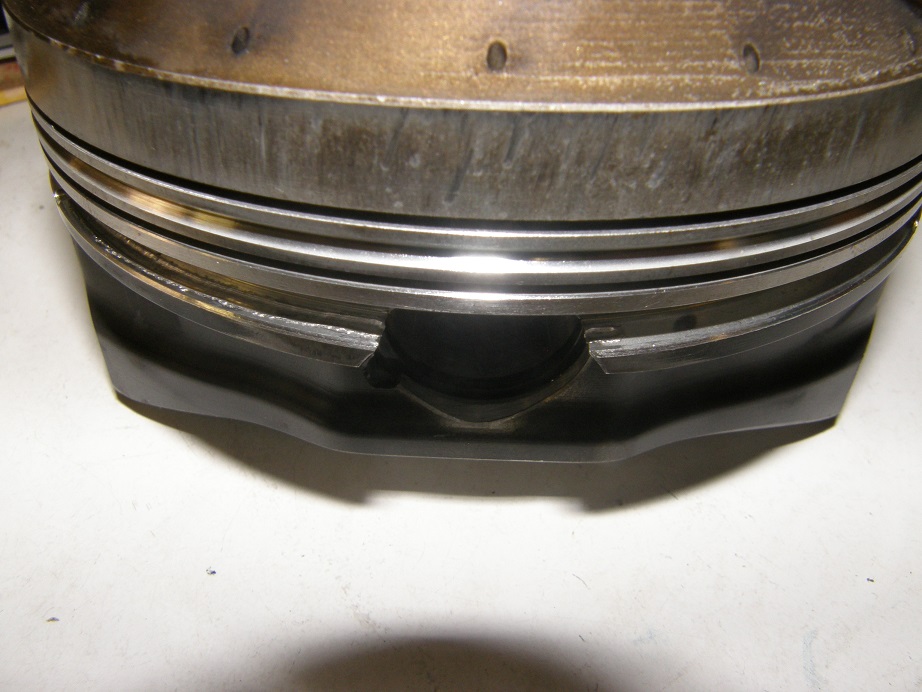
It looks like the oil ring rail rotated both ways, with the dimple digging a short groove in one side, and then a much longer groove in the other side. Here’s a picture of the end of the longer groove:
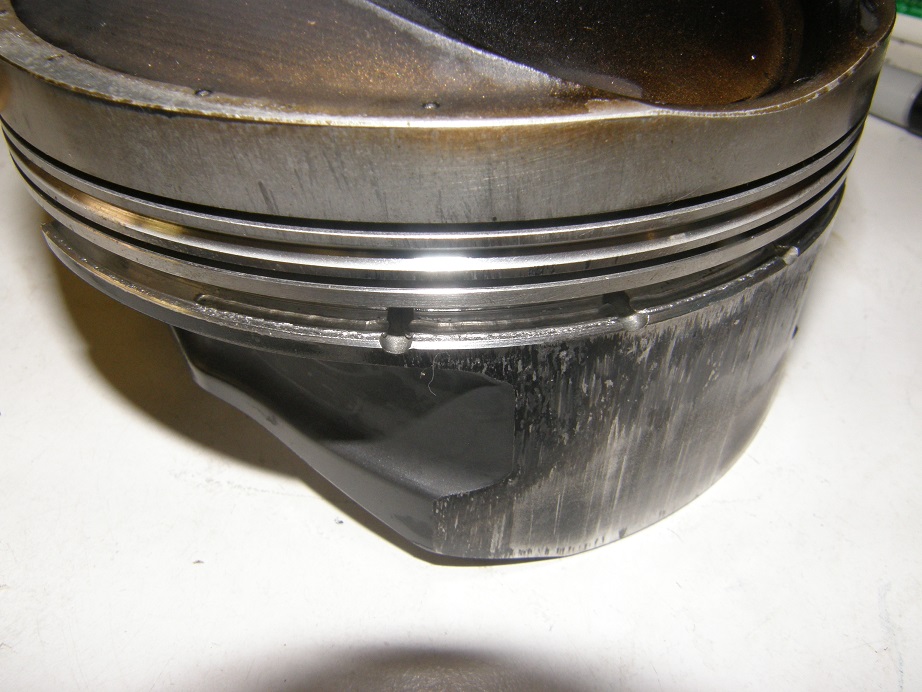
Not only that, but there was severe piston scuffing on that side of the piston! See the photo below:
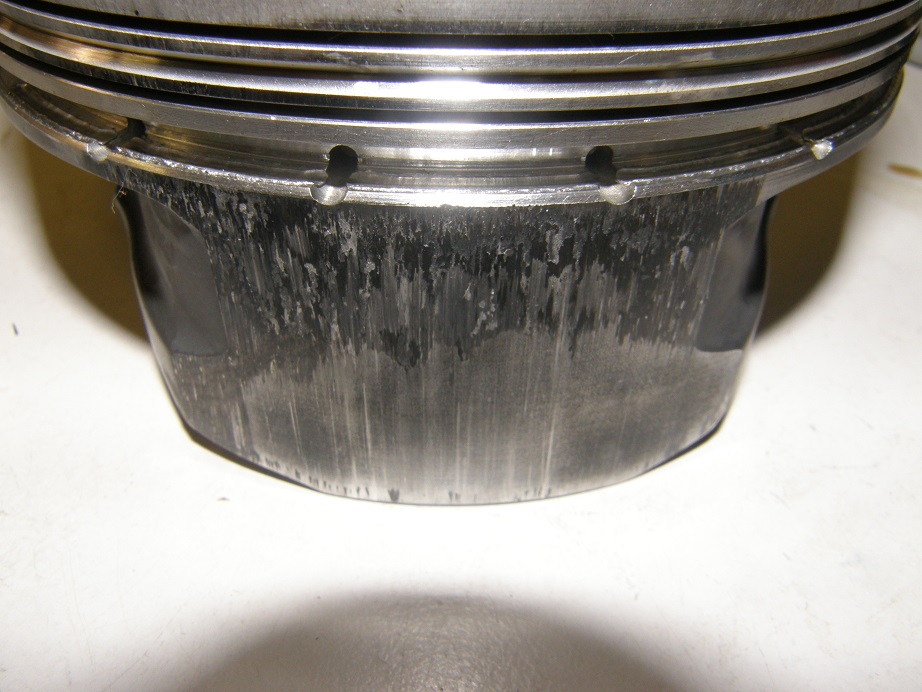
The oil rings were stuck because they were wedged between the raised oil ring rail and the ring land. I have never seen a failure like this before. I went ahead and continued to pull the piston rod assemblies, and remove the rods for magnafluxing. I found that to some extent, all 8 pistons had shown the oil ring rail movement. Three of the pistons showed minimal movement, around ½” or less, while the other five showed the groove from the dimple extending at least 90 degrees around the piston. Three of these five showed the scuffing problem. None of the pistons with minimal movement of the oil ring rail had any scuffing.
Anyone else seen this problem before? Looking at the bottom oil ring land it is thin at the start of the pin hole, and I think this would make it easier for that dimple in the oil ring support rail to start digging in to the oil ring land. The solution may be as simple as filing this sharp edge until it is thicker, which should make it more difficult for the dimple to start cutting into the ring land. But the whole situation seems very strange. I’ll bet I’ve assembled and disassembled a dozen engines with the oil ring support rails on the pistons, and I’ve never seen this problem before.
In any case, though, I’m thinking that I will need a new set of pistons for this engine, not just the one piston that I have already ordered. And I don’t know about the lead time for a new set. So, right now Drag Week 2016 is kind of up in the air for me; I may not make it with this car. I may have to go back with the Mach 1 if I can’t get this one together in time. I guess when I find out about the lead time for a new set of pistons, I’ll be able to figure that out. Of course, what would the lead-up to Drag Week be without some mechanical drama and a last minute thrash LOL! Here’s a picture of the car as it sits right now:

In the meantime this weekend I finally got around to solving the steering rack issue. With the oil pan off I was able to fit it over the K-member and see where I had space to put in some stops to fix the rack in place. A couple of simple brackets, one side fixed and one side with a screw for an adjustment, solved that problem.
Tomorrow on the Fourth of July holiday I plan to get started on the finishing bodywork on the two bumpers, so that I’m ready to try the fiberglass chroming process within the next couple of weeks. I’m going to try to have everything ready so that if I can get the pistons in a reasonable time period, I can still go with this car. We will see what happens. I will try to put up another update next weekend - Jay