This week I finally received my new sleeves for the Shelby block from Darton. Here's a picture of two of them:

Notice the groove in the outside of the sleeve at the bottom; this is for a 1/16" Viton O-ring. The sleeve on the left in the photo has the O-ring installed.
I had previously acquired the O-rings and had the block bored so that all eight sleeves would be the same diameter. This left me with fairly large holes in the aluminum casting in cylinders 3, 4, and 8. In order to make sure that the O-rings didn't snag on the holes in the cylinders I peened the edges of the holes over a little with a small ballpeen hammer. Then I set the block up in my powder coating oven to bring it up to temperature. I heat the blocks up to 300 degrees Fahrenheit to install the sleeves. Installation is normally pretty easy, because the sleeve is at room temperature and the block is hot. If you are removing the sleeves, the block and sleeve are both hot and so they both expand, making removal a little more difficult than installation. However, in this case I had the O-rings to contend with also, so the sleeves would have to be pushed into position against the force of the O-rings, rather than just sliding into place.
Complicating matters is the fact that the sleeves all have flat on them, where they fit together, and if the flats aren't lined up properly, the sleeves won't fit into the block. It isn't much of a challenge lining up the flats when the sleeves don't have the O-rings because when the block is at temperature the sleeves can be rotated easily by hand. However, the O-ring again complicates matters, and I expected it to be more difficult to rotate the sleeves if necessary, after they were installed.
Here's a photo of the block in the oven showing cylinders 5-8, prior to installation of the sleeves:
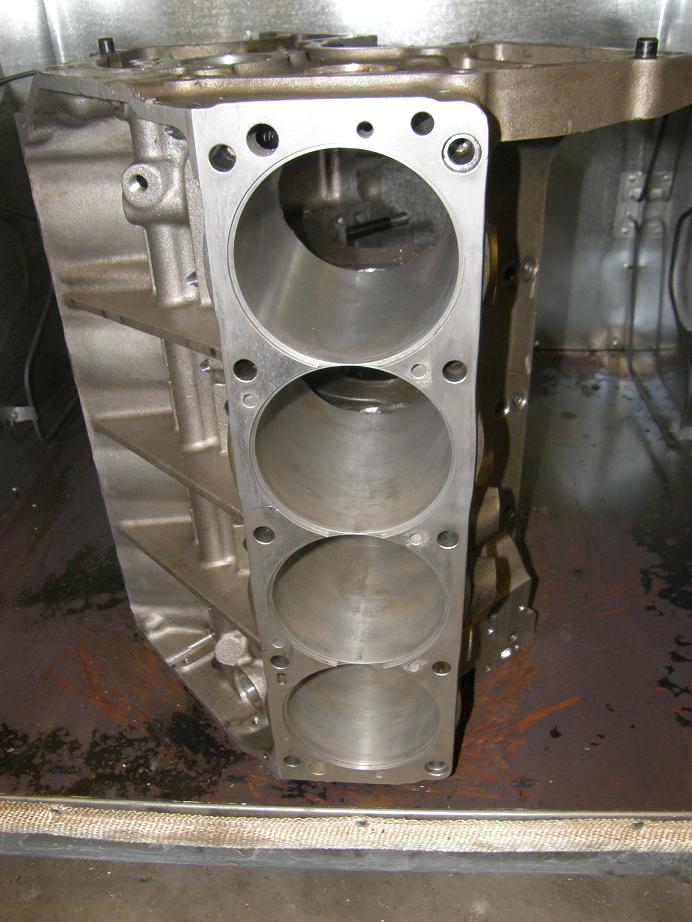
I let the block warm up for an hour before I started the installation. While I waited I cleaned all the oil off the sleeves, installed the O-rings, and lubricated each O-ring with a special lubricant designed to make installation easier. Finally I cracked open the oven and installed sleeve #8. It went in easily up to the O-ring, and then I had to use a deadblow hammer and a block of wood to push the sleeve into position. I tried to keep the flat in the right spot, but sure enough by the time the sleeve was nearly installed it had rotated somewhat. I tried twisting the sleeve to get the flat aligned correctly, but it wouldn't budge. After trying to tap the sleeve with a hammer to get it into the proper position, I decided to shut the oven door and let the block heat back up, and try to come up with a solution.
Eventually I decided that I could use a small vise grip to grab the flange of the sleeve, and then hit the vice grip with a hammer to rotate the sleeve in the bore. After ten minutes I opened the oven again, and after a couple of tries the vise grip and hammer approach worked, and I got the sleeve rotated into the correct spot. A couple more strokes with the dead blow and the sleeve was all the way in.
I continued with this technique to get the remaining sleeves put into position. In nearly all cases I had to grab the flange of the sleeve with the vise grip and rotate it so the flats would fit; the sleeves always wanted to turn a little while they were being driven in. But finally I got them all into the correct position. Here's a photo of cylinders 1-4, with sleeve #1 still not quite all the way into position:
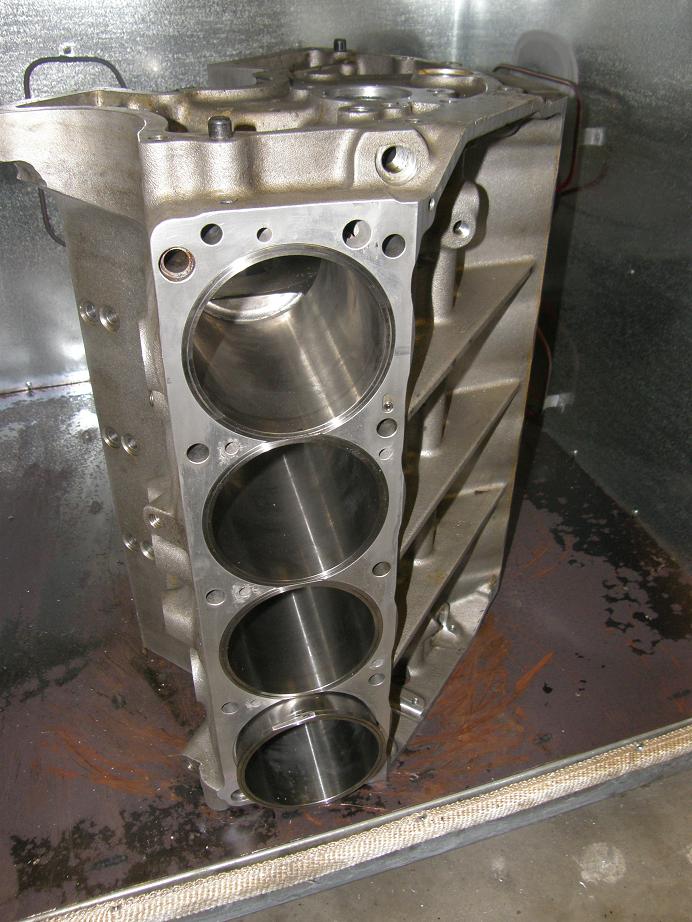
Now that the sleeves are installed, I will leak check the block this week. If I find any problems I will have to either replace the O-ring on that particular cylinder or come up with some other solution. Assuming the block is leak free, I will be ready to order pistons. When that happens, I'll be sending some of the existing pistons to CP, and maybe they will be able to shed some light on my piston to valve clearance issues.