It's been a pretty busy last week and a half or so. Last weekend I finally got around to pulling the wounded cammer motor out of my Drag Week car:
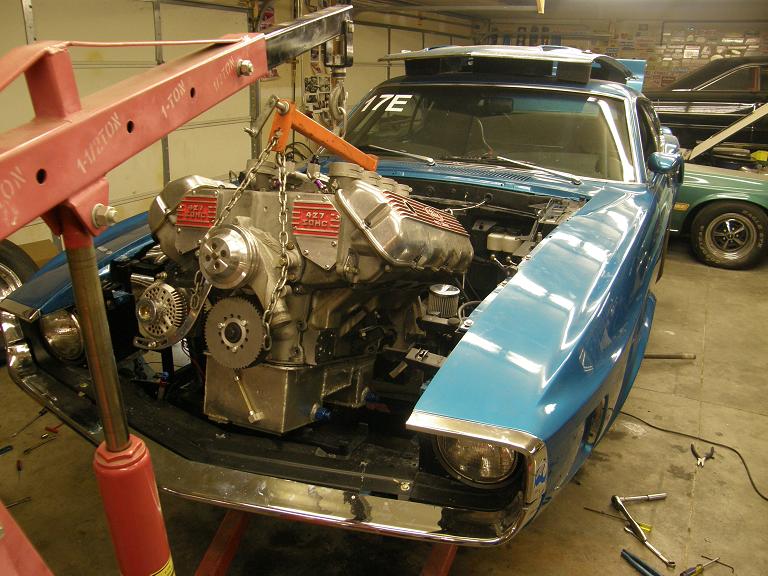
Teardown started last Sunday morning, and revealed some very unexpected and disturbing surprises. Everything looked good as I pulled the valve covers, oil pan, and front cover. The oil pan had a bunch of black crap in the bottom, and after looking at it for a while I concluded that it was probably some of that Moroso ceramic seal that found its way into the oil pan because of the coolant leak into the engine interior. On Drag Week, after the oil pressure started going down and the coolant temperature started going up, Joel and I had stopped the car at an exit and found the water in the oil, and decided to throw in the towel. We changed the oil and topped off the coolant in hopes of getting back to Topeka and our hotel under our own power, but after 20 miles on the way back, the oil pressure had dropped from 60 to 20, and I decided I'd better stop the car and get it towed. Coolant temperature at this point was still running 160 as normal, so I made the assumption that I was losing the bearings in the engine. The ceramic sealer remnants I found in the oil pan seemed to support this theory.
Next I pulled the rocker shaft and rockers off the engine. Everything looked perfect here; just as I'd put it together. Lash was good, roller wheels on the rockers all felt good, cam lobes looked perfect, etc. Here's a photo of the engine at this point in the disassembly process:
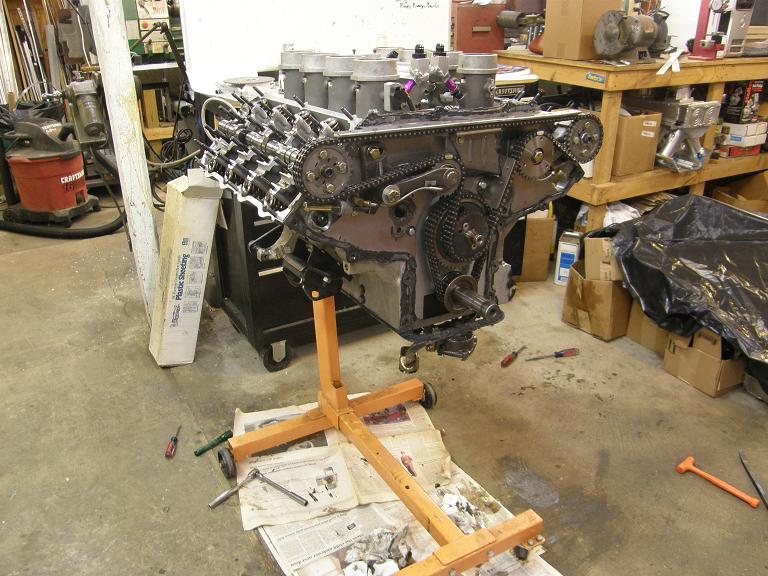
Next I disassembled the front end, again with no issues. The bearing in the Pond front cover looked fine, the bearings on the chain tensioner and fuel pump gear stand were fine, the Munro chain and all the gears looked fine. I had checked the chain tension and the cam timing when I first pulled the front cover and that was all fine also. So far, there was no indication of any reason for the engine to be down so much on horsepower. I also pulled the cams, and was surprised to see that the bearings looked pretty good. There was no indication of scoring or excessive wear, and the cam bearing journals looked fine. If I was circulating some abrasive material through the oil and losing the bearings, I would have expected to see some wear at the cam bearings. Hmmmmm...
Everything changed when I pulled the heads. I pulled the right head off first, set it on the bench, and looked at the combustion chambers. Everything looked normal. Then I pulled the left head and did the same inspection. Here's a photo:
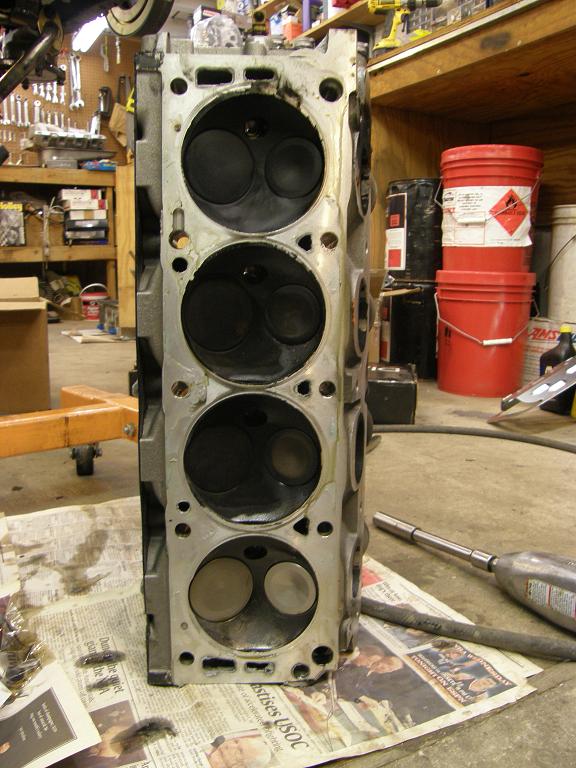
Look at how clean the #8 chamber is. It almost looks like it wasn't even firing! I couldn't believe that I would have missed that during the dyno pulls, but just to be sure I went back and checked the data, and sure enough #8 had normal exhaust temperature during the dyno pulls. Maybe water was getting into that cylinder? One important observation here was that this cylinder didn't look like this when I pulled the heads when the engine was on the dyno last summer. Maybe when I put in the new head gaskets I didn't get a perfect seal on that cylinder...
Next I went back and looked at the right bank pistons, and was shocked by what I saw. Three out of the four pistons showed evidence of piston to valve contact! The contact was all on the eyebrow portion of the intake valve relief, not down on the piston dome itself. Further, the contact was really, really excessive, with aluminum from the piston peeling out away from the contact area. This was a total surprise. When I had pulled the heads with the engine on the dyno last summer, there was absolutely no evidence of piston to valve contact on this engine. The heads had been planed .005", so this must have been the change that caused the contact, but .005"?? It looked like I had boatloads of contact, and that didn't come from a mere .005" cut on the heads.
Looking on the left bank, I saw some minor contact between the intake valve and the piston eyebrow on pistons 5 and 8, but nowhere near as extensive as on the three pistons on the other side. Piston number 4 was definitely the worst of the bunch. I decided that I'd better center punch all the valve locations on the pistons, so I disassembled the heads and removed the valves, then took a junk valve, cut the head off, and sharpened a point on it on my lathe. I put a degree wheel on the crank and found TDC on number 1, then reinstalled the heads on each side and working around the engine rotation, center punched each piston with the pointed valve stem when it was at TDC. Then I pulled the heads and measured the distance from the center point to the contact point on the pistons. The dimension was 1.230". Well, this didn't make sense; the valves in this engine are 2.300", so the valve shouldn't extend any further out from the center point that 1.150". Yet I had contact at 1.230". Hmmmm....
I rocked the pistons in the bores back and forth at TDC, and found that the top of the piston would move about .050" laterally, rotating on the piston pin. This could explain part of the dimensional discrepancy, but not all of it.
I left the short block together, still puzzled by all this, and early this past week I gave my pal Blair Patrick a call. Blair suggested that maybe the closest point of approach of the edge of the valve to the piston eyebrow wasn't at TDC, and thought I should center punch one of the pistons at a few degrees before and after TDC to see if the valve centerline moved further inboard at some point. After hanging up with him I drew a few sketches of the piston and valve relationship, and with the cammer valve and piston geometry I couldn't see any way that the valve centerline would move inboard from TDC. But it was worth a check, so I re-installed the right head and center punched #4 at -30, -20, -10, +10, and +20. Furthest inboard position of the valve centerline was definitely at TDC. Here's a shot of the piston with all the marks on it; the line scribed in the top of the piston points toward the center punch mark at TDC:
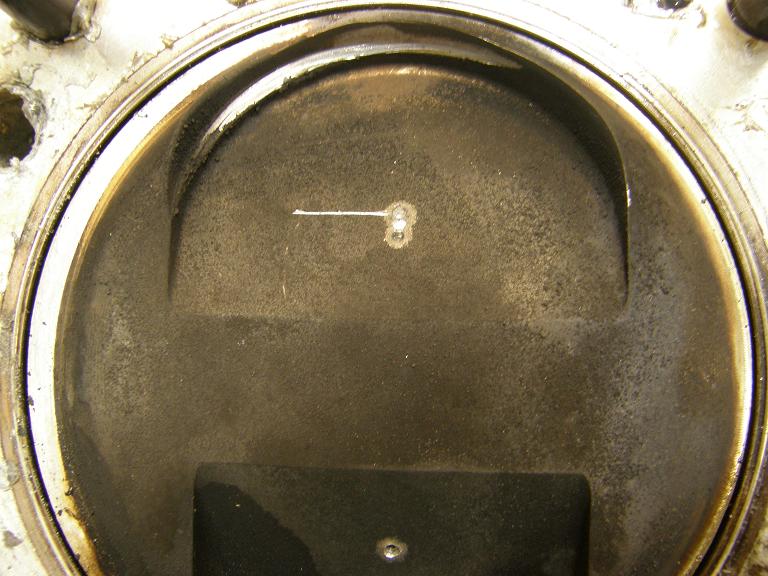
Tuesday night I pulled the short block the rest of the way apart. Surprisingly, everything looked good. In particular, the bearings looked perfect! Another mystery; with new oil in the engine on my last 20 miles of the Drag Week drive, oil pressure was dropping. Why? The bearings and crank looked beautiful.
I checked the cylinder bores and they were out of round by .001" or .002" in some cases, but the measurement was done without a torque plate, so they might have still come back into line when the head studs were torqued. I had been hoping to find an obvious answer for the loss of 150 HP on the dyno with this engine, but it was not apparent on the short block teardown. (I don't think that the piston to valve clearance issue is related to the horsepower loss, because the loss was the same before and after the headwork and new head gaskets last summer).
Wednesday I stopped up at R&R Performance and asked my pal Bryan up there what he thought of the piston to valve contact issue. I brought along the #4 piston, and also the #4 intake valve. With as hard as the valve was hitting the piston, I figured that this valve had to be bent, but it didn't really look like it, and I wanted Bryan to check it. Sure enough, the valve was not bent. Go figure. Bryan measured the valve then set up a scribe compass, and put it in the center punch hole in the piston, then scribed a line around the piston dome to see where the valve should be. It sure looked far away from the contact point. Here's a photo of the top of the #4 piston:

The scribed line shows that not only is the piston contact point further outboard than the valve head is, but it is also offset to one side. The pistons look like they are made correctly, judging by the center point on each one. Just for grins I checked to cracks in the heads that may allow the guide to move around somewhat, but found nothing. Guides were nice and tight, too. Hmmmm...
With this mystery lingering, this weekend I decided to pull the sleeves out of the block. When I had originally offset bored this block we had broken through into the water jacket in cylinders 3, 4, and 8. After installing the sleeves I had used a chemical sealant called Seal-All, available from Goodson, to seal up these leaks. It held from 2008 through 2010, but apparently failed in the past year. As a result I expected to see a lot of rust on the sleeves in cylinders 3, 4, and 8. This would make them more difficult to remove. To remove the sleeves you have to heat the block up to 300 degrees and then tap the sleeves out with a brass drift from the crankshaft side of the block. As expected, cylinders 3, 4, and 8 were difficult to remove, and all three showed evidence of leakage. Here's a shot of the block with the sleeves removed on the left bank, showing the clean aluminum casting in hole #7, and the rusty residue left inside hole #8:

However, I was surprised to see that on the right bank, there was rusty residue left inside holes #1 and #2, in addition to #3 and #4. A look at the outside of sleeve #1 showed at least a partial explanation:
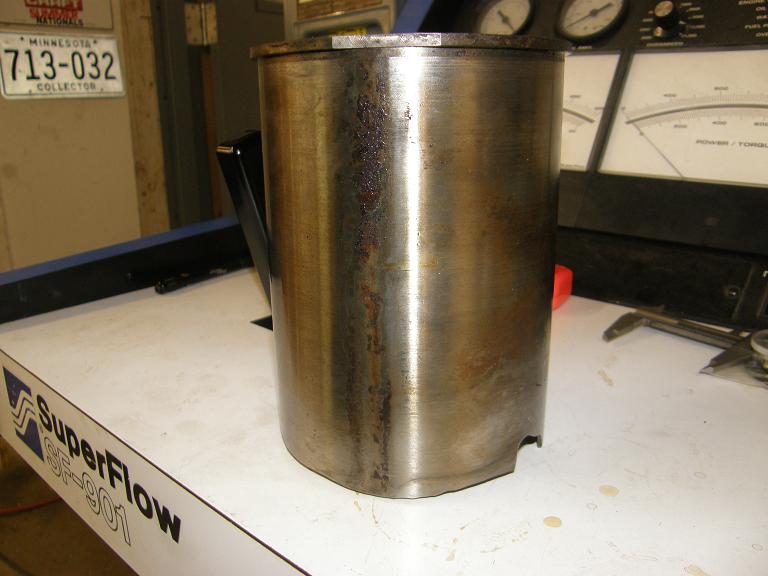
It looks like I have another head gasket leak here, and water is being forced down between the sleeve and the block, and out the bottom of the sleeve. You can see evidence of the same leak in cylinder bore #1:

The leak in number 2 is a mystery at this point. I think I will put a torque plate on this side of the engine, with a head gasket, and pressurize it to look for any leaks in the block casting in the #2 bore.
Short story - the engine was leaking water like a sieve, both in the expected places, and also in some unexpected areas involving the head gasket. Was this the reason for the lack of power production? I don't know, but it sure didn't help matters. I'm looking at a few different options to more positively seal this block up, including either welding the block or O-ringing the bottom of the sleeves. Neither option is perfect, but I think I can get 'er done. Then it will be time for new sleeves, new pistons, and re-assembly of the engine. Hopefully by then I will have figured out the deal with the piston to valve contact, and can get a new set of pistons built that will eliminate this problem. I will post more under this topic as I get further along down the road to rebuilding this engine...