Got back on the high riser project this week, and managed to get most of the tough stuff done on the intake manifold. I still have a lot of work to do on it, but the initial welding is complete, and thanks to my jig and carefully machined parts, it seems to have weathered this part of the build just fine, with no extreme warping to worry about.
During the evenings this week I spent some time trimming up the runner assemblies in the mill to make them all identical, so that I would have minimal problems with fit. I also bolted the port plates and the intake manifold base plates to the heads, and used some sand rolls to remove the CNC tooling marks inside the runners, and smooth everything out so they lined up perfectly with the ports in the heads. It was cool to be able to do this; when I got done it looked like the port runners were a single piece, except where the gasket was between the port plates and the heads.
Friday night with a full weekend in front of me I spent the evening tacking the runners to the intake manifold base plates. I wanted to be able to move them around a little if necessary, so I didn't weld them completely, just ran about a 3/4" long bead along the bottom of the runner to hold it securely in place for fitting the plenum plates. Then I bolted the heads, port plates, and manifold base plates to the engine, with the head gaskets installed but without the intake manifold gaskets. My thinking here was that I wanted to make the intake manifold wider than necessary, to give me some room to machine the manifold base plates in case they warped during the welding operation and needed to be planed. Here's a couple photos of the engine with all this stuff installed:
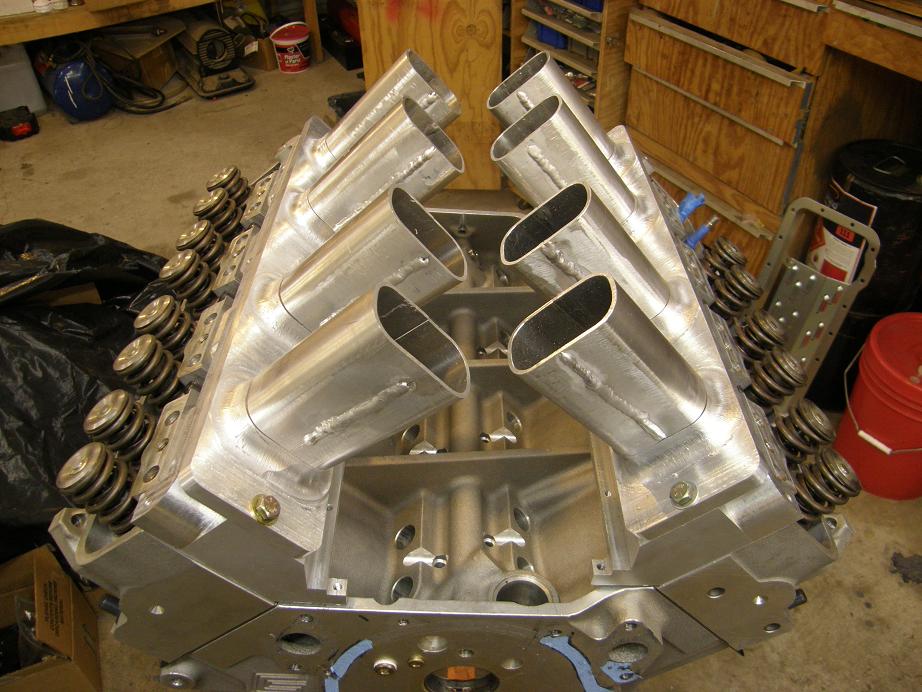
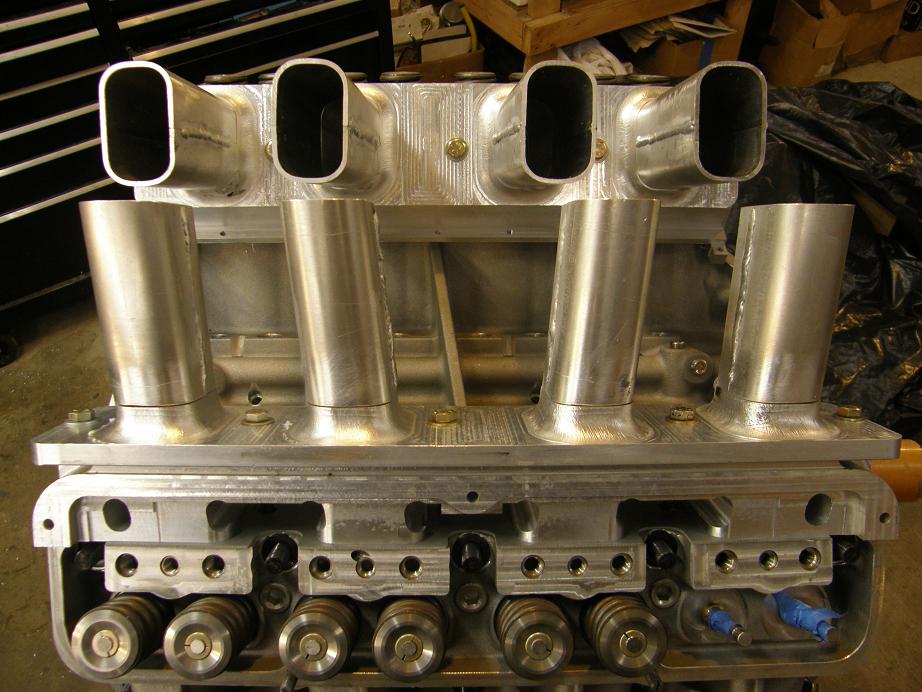
Saturday I started by taking my two plenum plates, which I had previously welded together into a V, and tried to fit them on the runners. They were close, but sat up about 1/8" too high. If you look at the previous photos I posted you can see that the plenum plates have the runner entrance machined into them, with about 1/4" of each runner extending out of the plates, to make welding to the formed runners easier. I took the welded plenum plate and stuck it in the mill, and cut .125" off the extensions on the plates. Back on the engine the plenum plates now fit almost perfectly.
I weighted down the plenum plates on the runners to keep them stable, and started welding the runners to the plenum plates. After getting all eight runners tacked, I continued welding as far around the runners as possible, both up at the plenum plates and down at the manifold base plate on each side. When I finally got done, about 2/3 of the welding was finished.
My original plan had been to unbolt the manifold from the port plates at this point, and use it as a pattern for a jig to be used for welding the remaining seams. I had a brief urge to just tear the manifold off the engine and finish welding it on the bench, without the benefit of the jigs, but after thinking it over for a little while, and remembering how much time I had into the manifold port plates, runners and plenum plates, I decided I'd better not chance it. So, I grabbed the 4" angle iron and 2X3 square steel tubing I'd purchased for the jig and set about building it. After cutting the steel to length I put the 4" angle iron in the CNC machine and drilled the holes to match the manifold base plates, then tapped the holes for 3/8-16 bolts. Finally I bolted the partially welded intake to the angle iron, set it on the square steel tubing, and welded the angle iron to the square steel. Here's a photo of the partially welded intake on the jig:
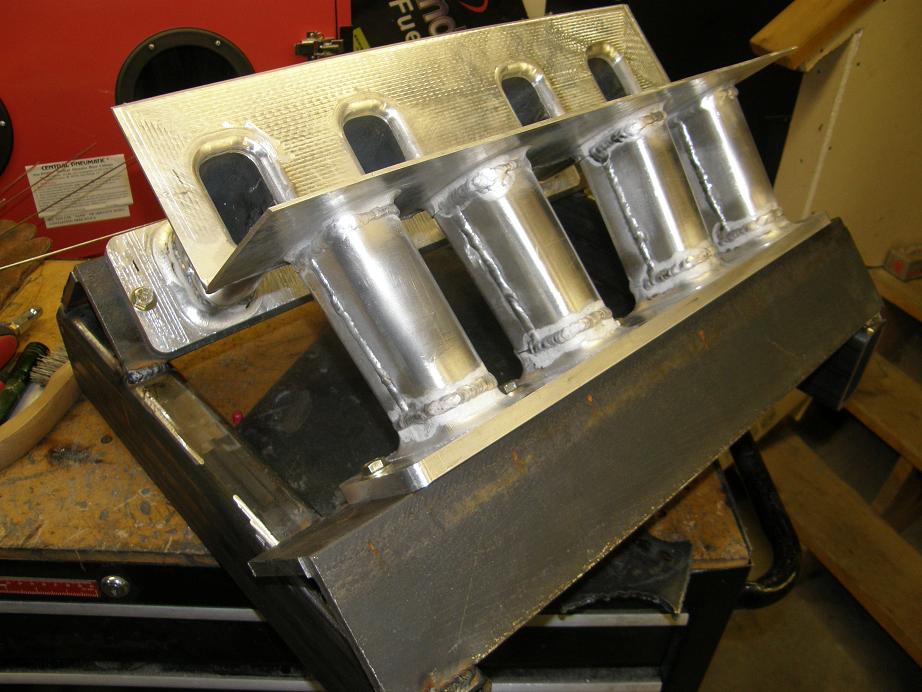
Now that the jig was done I was able to complete welding on the intake. I flipped the jig over to get access to all the runners for welding. Just like on my SOHC sheet metal intake, this gave me excellent access for welding, and it was not problem to get the manifold welded up.
Over the course of the last few weeks I've been rethinking the oiling system on this engine. I had planned to use a stock type oil pump, and drive it with a "half distributor", which would be a partial distributor shaft that bolted into the distributor's location, and connected the cam gear on the cam with the oil pump drive shaft. One problem with this design was that where the half distributor (or a full distributor for that matter) came through the intake manifold, there was always a vacuum leak when I tried to run a crankcase vacuum pump. Bill Fowler had been telling me about his Peterson external oil pump, so I decided to look into one of those. I liked what I found out; the pump sucked out from a line at the bottom of the oil pan, but also could be ordered with some scavenge stages that essentially created crankcase vacuum. Using this setup I could eliminate the half distributor and the external vacuum pump, and also the potential vacuum leak at the half distributor location in the manifold. I made the decision to go forward with this setup. As a result of that, I decided to machine a new valley cover plate, one without the distributor hole, to completely seal up that potential leak. Here's a photo of the new valley cover plate installed on the engine, with the port plates:
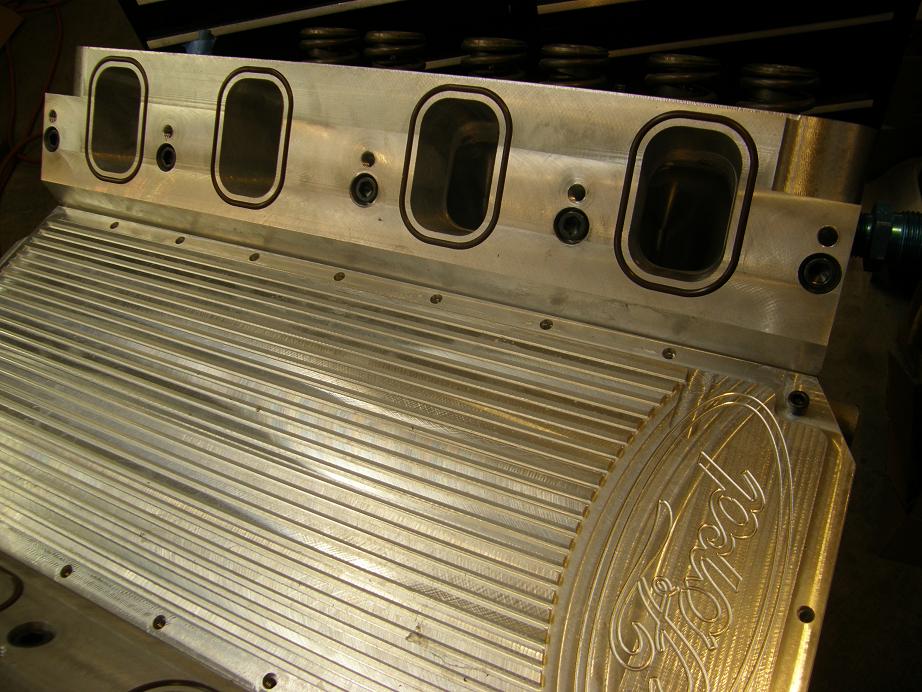
In the photo above you can see that with the extra room created by the lack of the distributor hole I was able to make the Ford logo bigger, which I thought was pretty cool. Also you can see the Viton O-rings installed on the port plate, in preparation for installation of the manifold.
Finally, after the manifold cooled down today I bolted it back onto the engine to see how it fit after the final welding. It appeared that the mating surfaces were still pretty flat, but that the entire manifold had shrunk just a little bit. The ports and bolts still lined up perfectly though, and I still had the port plates installed without the .060" thick intake gaskets. So I think that once they are installed, the manifold may fit pretty well as is. Worst case it looks like I might have to take .010" or .020" off the mating surfaces. Here's a photo of the manifold installed on the engine:
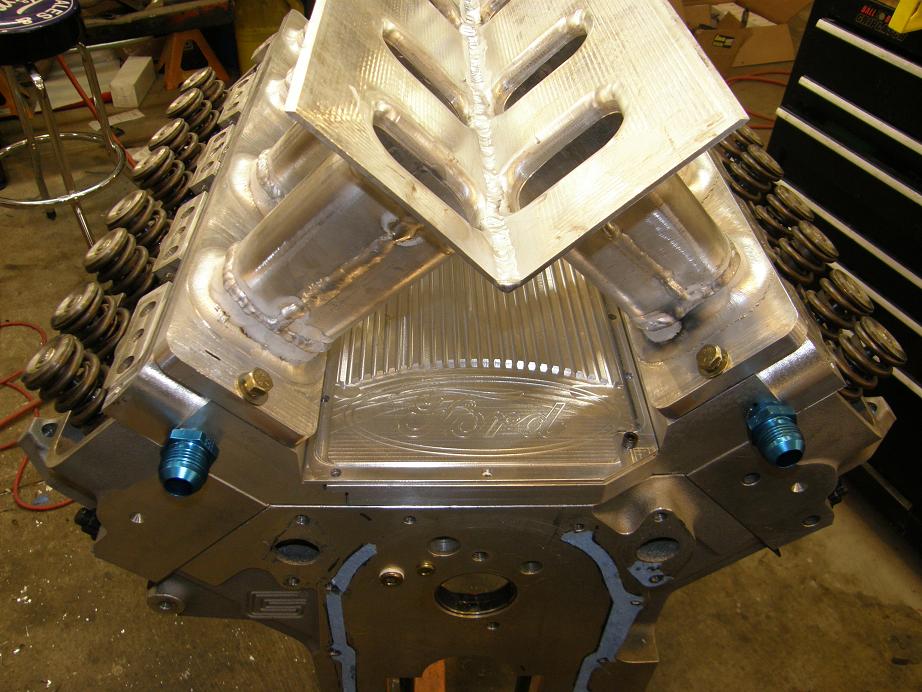
Next up is the finish porting work inside the runners where they meet the plenum plates and port plates, and then installing the injector bungs and welding them and the fuel rail brackets in place. Then I'll be able to finish the plenum of the intake and start thinking about the top plate to mount the Dominator throttle bodies. I'm looking forward to seeing the whole thing put together! I'll post more photos as I make progress.