More progress on the sheet metal intake over the long New Year's weekend. It took me longer than I expected to get the plenum plates machined, but after three test plates I finally got it right, so I put the full size stock in the CNC machine and ran the program. Unfortunately the translation from small test plates to the full size plate revealed an error in the program, and I also made a setup error on the first plate, but it still turned out to be usable. The second plate came out perfectly; here's a couple of photos:
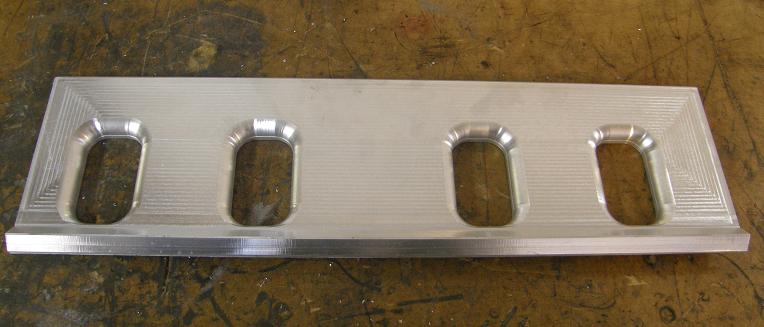
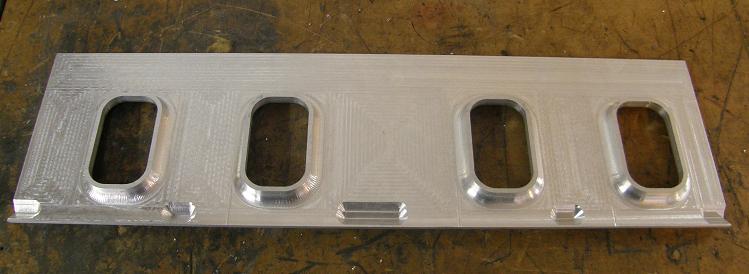
Given the runner length I wanted for the manifold, the plenum had to have a gap between the runners. Rather than extend the plenum down into a point below the runner entry (which I've been told doesn't work well because fuel tends to puddle in the vee), I machined the plates with a flat bottom that is at the same level as the bottom of the runner. The CNC program machined almost all of this area, but I had to finish it by hand with an abrasive porting roll in my die grinder. With the flat bottom, I was able to incorporate some tabs at the bottom of the plenum plates which allowed them to be bolted together. I figured this would make fixturing the intake for welding much easier. Here's a couple photos of the plenum halves bolted together:
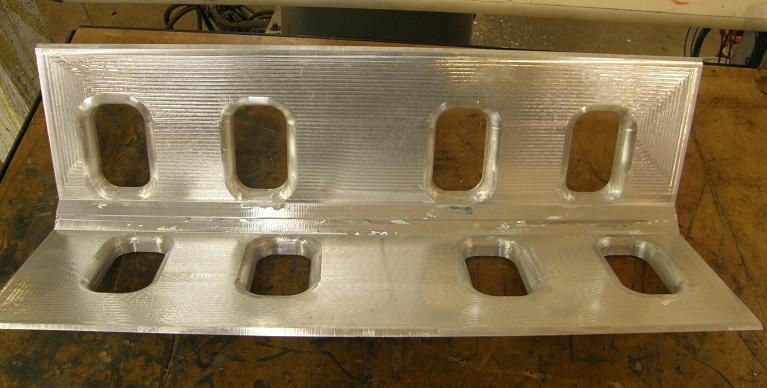
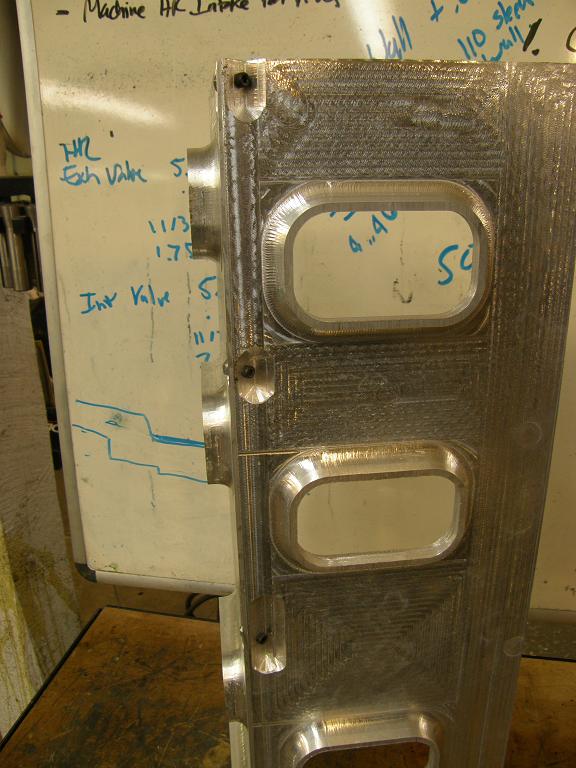
Once the plenum plates were finished I started on the runners. Previously I had made some machined aluminum blocks that allowed me to bend the runner shape, half a runner at a time, using 1/8" 5052 aluminum in my hydraulic press. When I pulled these out of the drawer and measured them, though, I realized that they had not been built using the correct radius for this new manifold design. So the runners weren't going to match up well with the ports in the corners. I decided I'd rather make up some new blocks with the correct forms so that the runners would be right. This wasn't too tough to program into my CNC machine, but in order to make the blocks where the runners were pressed as smooth as possible, I had to take very fine cuts with the tool, every .025" down a 6" length for both the positive and negative forming blocks. This took a long time on the machine, but finally yesterday the blocks were done.
Today I started on the runners themselves. I had previously cut 16 aluminum squares, 5.5" on a side, out of the 1/8" thick flat 5052 sheet. One by one I put them in the press with the forms and bent the runner halves into shape. Here's a picture of one of the runners being bent, and a bunch of them completed and ready to machine sitting on the bench:
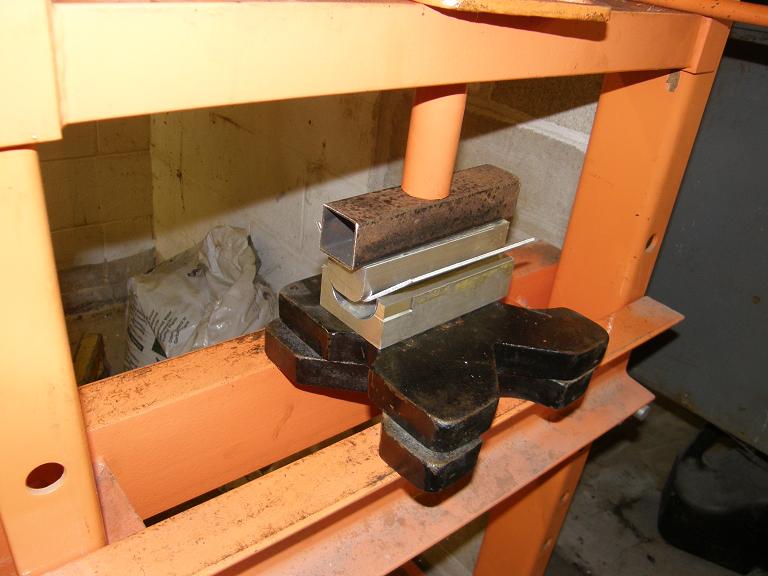
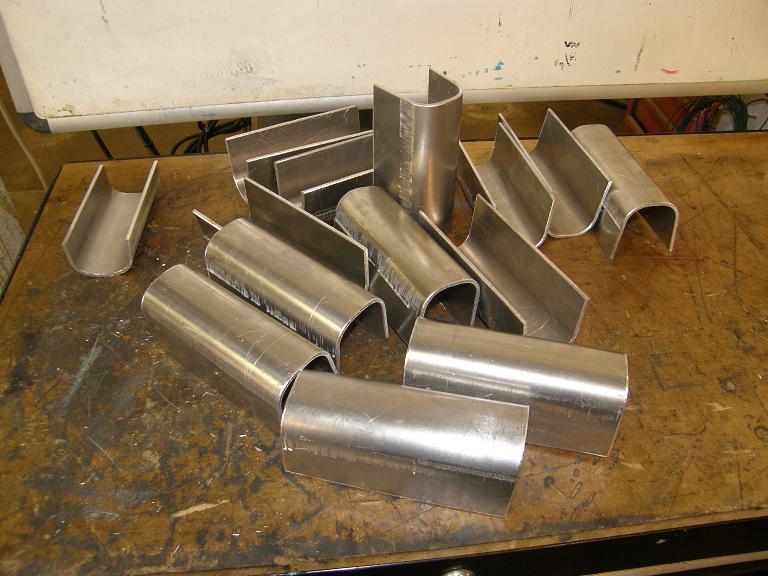
Bending the plates didn't take long, and I had previously decided that the easiest and most consistent way to trim these plates to the correct size would be in the CNC machine. It didn't take long to write a few little programs to do this, and pretty soon I was machining the bends with the correct angles on the end to keep the runner angle correct with respect to the head port, and also to put a taper on one bend of each pair, to get a slight taper to the runner itself. I ended up having to write six different programs in order to get all the combinations handled, and in fact I still have four bends to finish the machining on, but this all worked pretty well. Late this afternoon I stopped work on the CNC and took four of the runners over to the welding bench. I clamped them together prior to welding and they all fit together real well. I welded the seams on both sides of each runner, and then took them over to the other manifold parts already mocked up on the engine for a test fit.
The test fit did NOT go well LOL! I taped the four runners onto the base of the intake, but when I tried to fit the plenum plates on top they were way, way off! What the heck? I looked at the setup for 10 minutes, trying to figure out what was wrong, but everything seemed to be right. The plenum plates just wouldn't fit.
Finally I pulled up the drawing CAD file that I had made for this intake, and that I was basing all the dimensions off of. First thing I did was recheck the measurements from front corner to front corner of the engine, where the end rail meets the heads. I could have kicked myself; the measurement was just about 10.5", but I had drawn it as 11.5" on my drawing! That was the base dimension for calculating the runner length and designing the plenum, and it was either a measuring error or drawing error on my part that caused the problem.
Fixing this problem was going to be one of two choices. I could either shorten the intake runners until the plenum set down in the correct position, or I could section the flat portion of the plenum and remove one inch, so that it would fit down properly on the runners as they were. I decided to pursue the latter course, because I had messed up the machining on one of the plenum plates anyway, and the part that was messed up was the flat portion. Plus, I didn't want to reduce the runner length because I had that right about where I wanted to get the manifold to tune at 7500 RPM. So, I unbolted the two plenum plates and took them over to the bandsaw, and basically cut the middle flat section out of the plates. Now of course I didn't have bolts holding the plates together, so I took some steel blocks and clamped the plates to them in the correct position, and then welded along the bottom of the seam from the outside of the plenum to stick them together for easier handling.
Back at the engine mock up the modified plenum fit just fine, so I taped it in place to get some pictures. This thing is finally starting to look like a manifold:
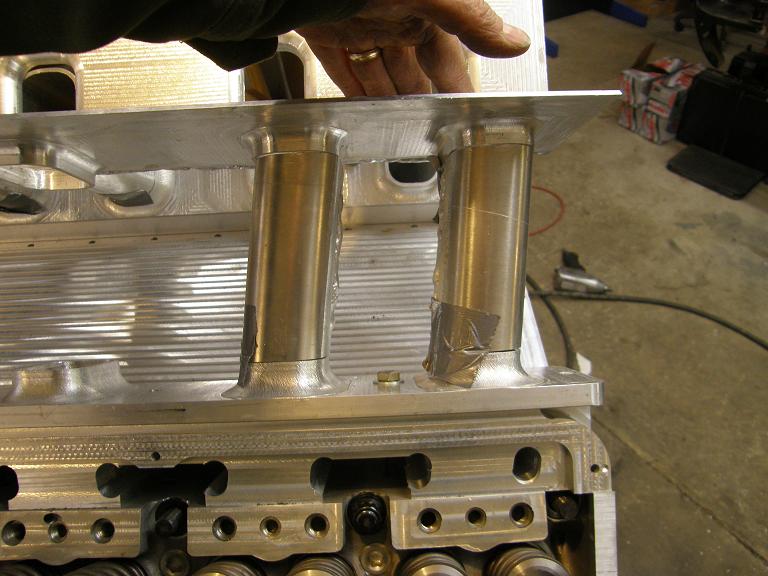
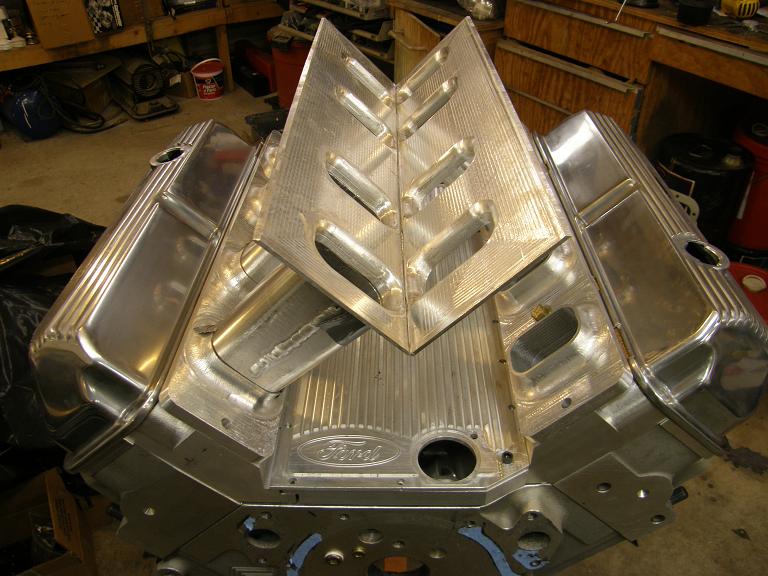
This week I should be able to get the remaining four runners machined and welded together, and be ready to tack up the manifold. Before I do that I have to disassemble the valves from the heads, bolt the plates on, and use a sand roll to smooth out the CNC porting marks and match the plates up to the ports in the heads. Then I should be able to tack the whole thing together on the block, before removing it for final welding. I'm planning on using the tacked up manifold as a guide to make the same sort of steel welding fixture that I made when I built my intake for the big SOHC. This will make sure that the manifold stays as square as possible during the welding operation.
Despite making pretty good progress on this intake, it is still taking a lot longer than I had originally anticipated. What a surprise LOL! Hopefully I can get this thing completed sometime in January, and go on to some of the other engine projects that I need to get finished before spring...