Here's a couple pictures of one of the coolest engines Ford ever built:
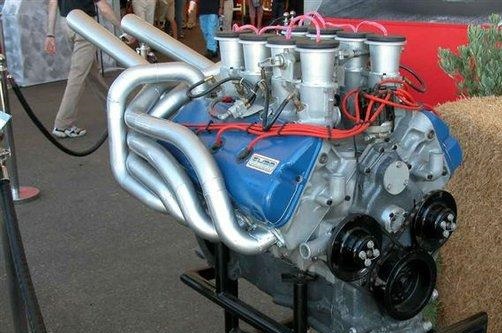
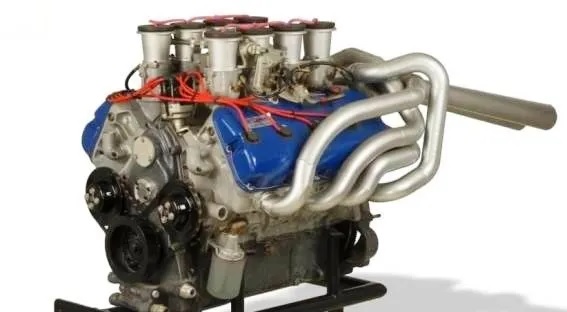
For those who don't know anything about this engine, here's a little background. After winning LeMans in 1966 and 1967 in GT-40s with FE 427 engines, Ford was planning to go back to LeMans in 1968 with a new engine. This engine was very loosely based on the new for '68 385 series engine, but had dramatic engineering changes compared to the production engine. The engine had 2 intake valves and one exhaust valve per cylinder, and the valves were pushrod actuated with two different camshafts in the block, one cam with 16 lobes in the normal position to run the 16 intake rockers, and a second cam in the block above the first which ran the 8 exhaust rockers. The exhaust pushrods ran horizontally from the cam to the exhaust rockers.
Built into the cylinder heads were the injector stacks, so that no traditional intake manifold would be required. The presence of the stacks apparently reminded Ford engineers of a calliope pipe organ, which is how the engine got it's nickname. The bundle of snakes headers shown in the pictures were designed to fit the Ford GT-40 Mk IV chassis. The engine also featured a dry sump system incorporated in the pan, which was claimed to provide crankcase vacuum in addition to oil pressure and control.
The engine was 427 cubic inches in order to meet LeMans rules, but prior to the 1968 LeMans race, the sanctioning body outlawed 7 liter engines, making smaller engines mandatory. As a result the project was stillborn after the rule change, and Ford corporate bailed on racing at LeMans (although independent teams won again with GT-40s in 1968 and 1969, running small blocks). The Calliope engine itself disappeared from view for many years. Apparently only two of the engines were produced, and only one is still existing, at the Ford museum in Dearborn. Dyno testing by Ford back in the day showed the engine delivered 630 HP, which would have been a big step up in the LeMans cars compared to the FE engine.
My friend Dan Schoneck learned about the Calliope engine a few years ago and after asking a bunch of questions of various contacts, found out that the original foundry tooling for the engine was still in existence. From what I understand the tooling originally went to Holman and Moody, and then was sold to a well known parts manufacturer on the west coast in the 1980s. I don't have permission to reveal who had the tooling, but most of us would know his company. In any case, Dan finally found out who had the tooling, and arranged to buy it all; he came back with it this past summer.
Over the last 12 years I've developed a lot of foundry experience and tooling contacts, and this was one project I was very interested in getting involved in. So after getting a look at the tooling Dan brought back, and figuring out what we had, I volunteered to bring it to my foundry's attention and see if they would be interested in casting it. This was a bit of a sales job, because the volumes of this project were not going to be high, and working with tooling from the 1960s would certainly be a little risky, but I put together a presentation for the foundry and they were interested enough to give us the go ahead for casting the cylinder heads. I also got my local pattern shop involved, because I know the owner there very well and he loves doing this kind of stuff. The owner has years of experience designing the feed system which channels aluminum into the mold properly. This is a critical part of any aluminum casting and was going to be required because the tooling was prototype tooling from Ford, and did not have sprues, risers, gating, or any feed system that normal foundry tooling has. This meant that Ford originally cut all these features into the sand cores by hand. My pattern guy has the experience to do the same thing, so he is an important part of the project.
Dan delivered the tooling to the foundry a couple weeks ago, and yesterday we got started on trying to pour a cylinder head. The Ford tooling is super cool; most of it is hand made from mahogany, and each tooling box is labeled with a Ford XE number. Apparently the XE number for the Ford Calliope cylinder head is XE-139612. See the tags on the cylinder head end core box below.
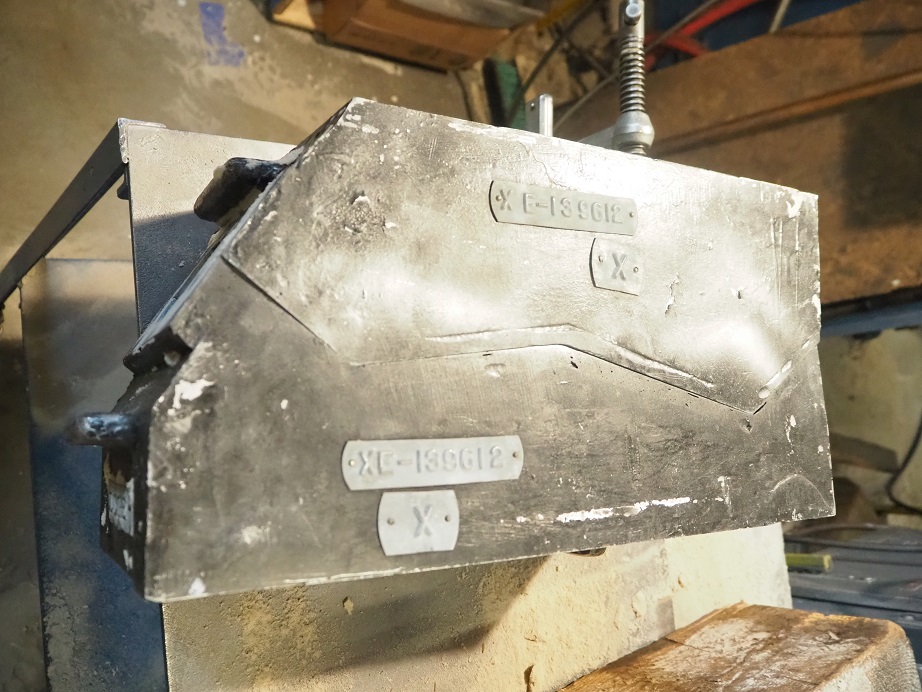
Pictures of some of the sand molds are below. This is the drag, which is the bottom of the mold:
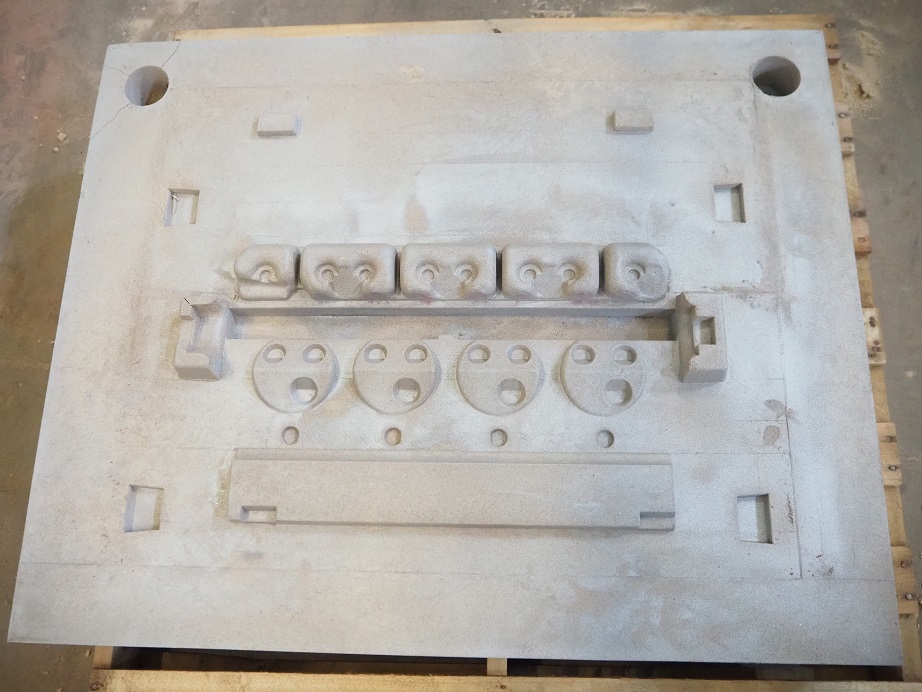
The intake port cores are individual, and look like this:
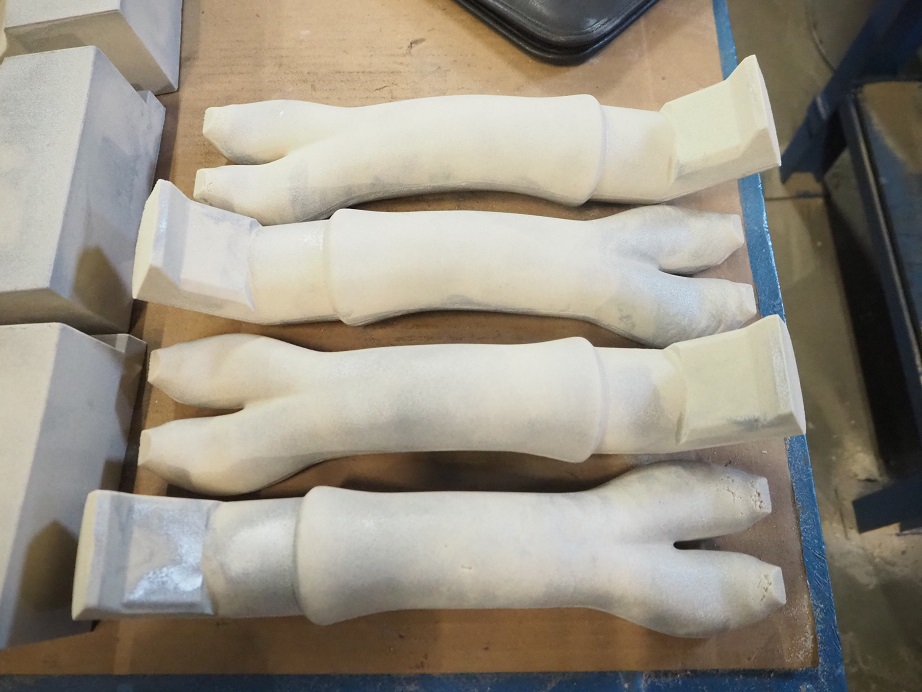
The exhaust ports cores are all molded in a single piece. It's interesting to see how the port widens out into an oval shape as it exits the head:
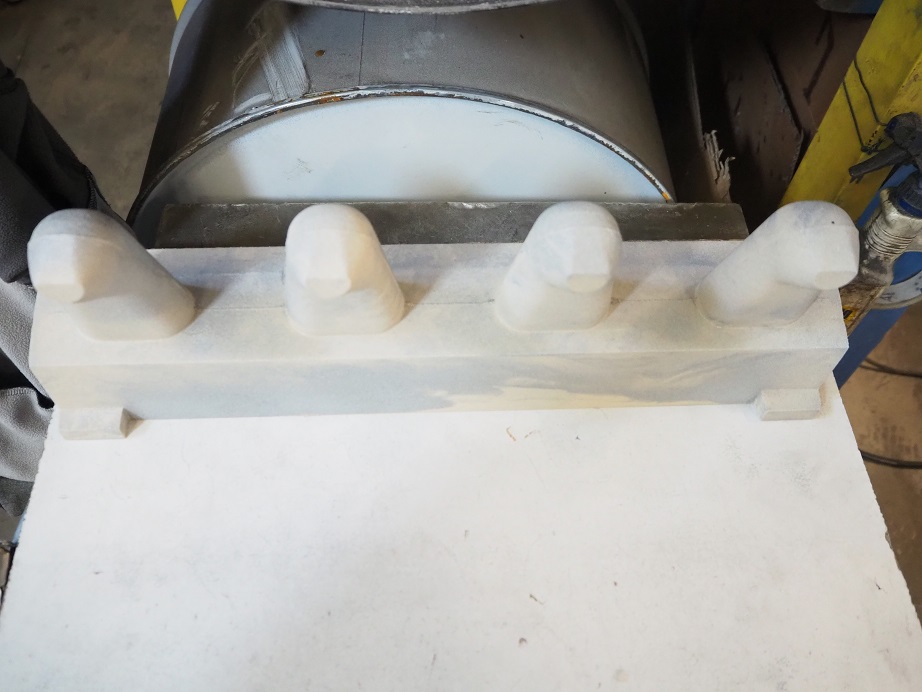
There are also cores for each end of the cylinder head, and the bottom of the intake runners. We assembled all these parts on the drag to get a look at how it all fits together:
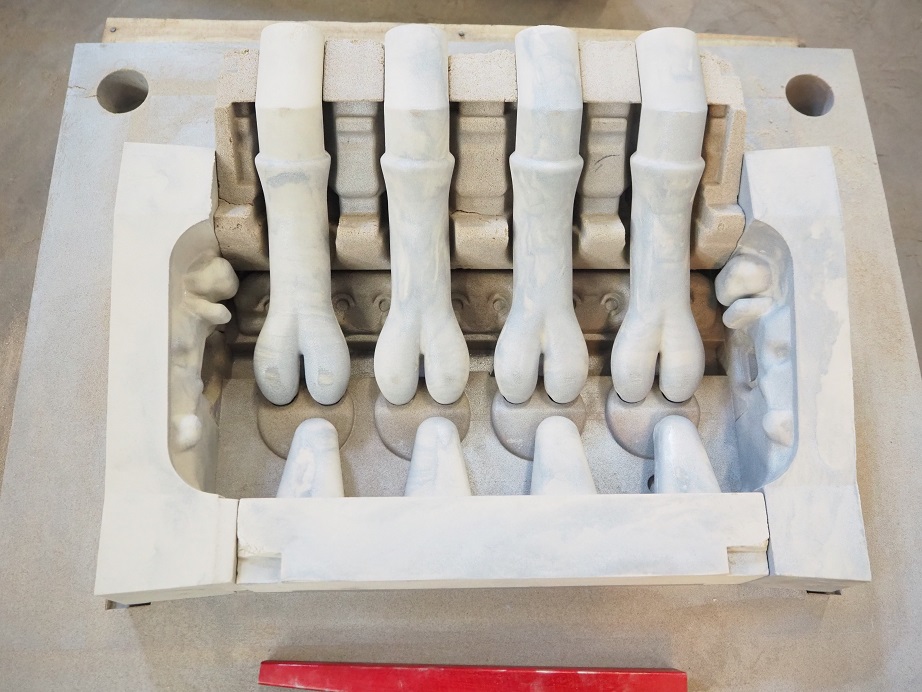
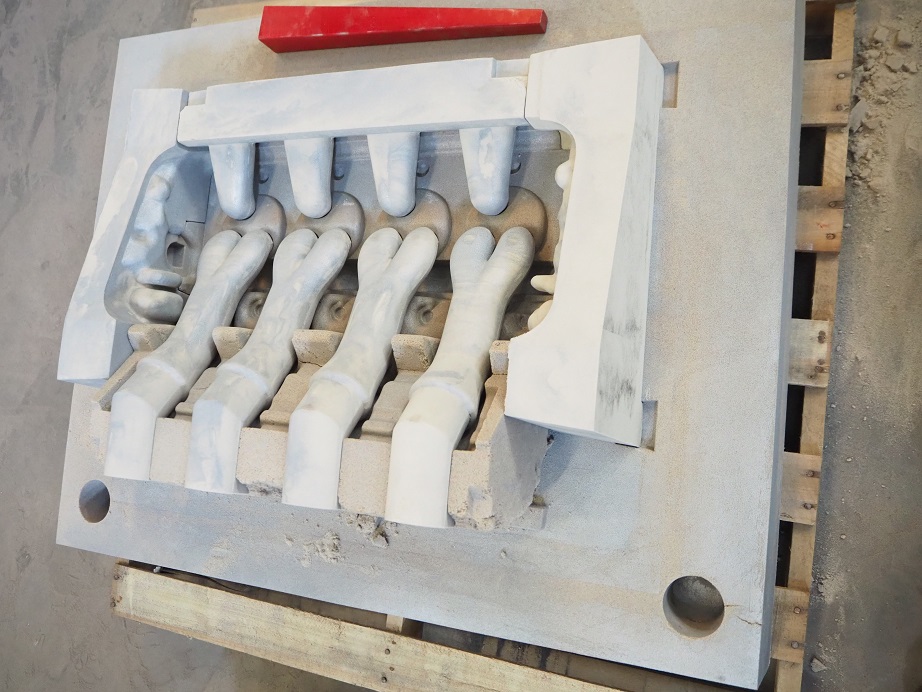
The core below closes over the top of the previous mold:
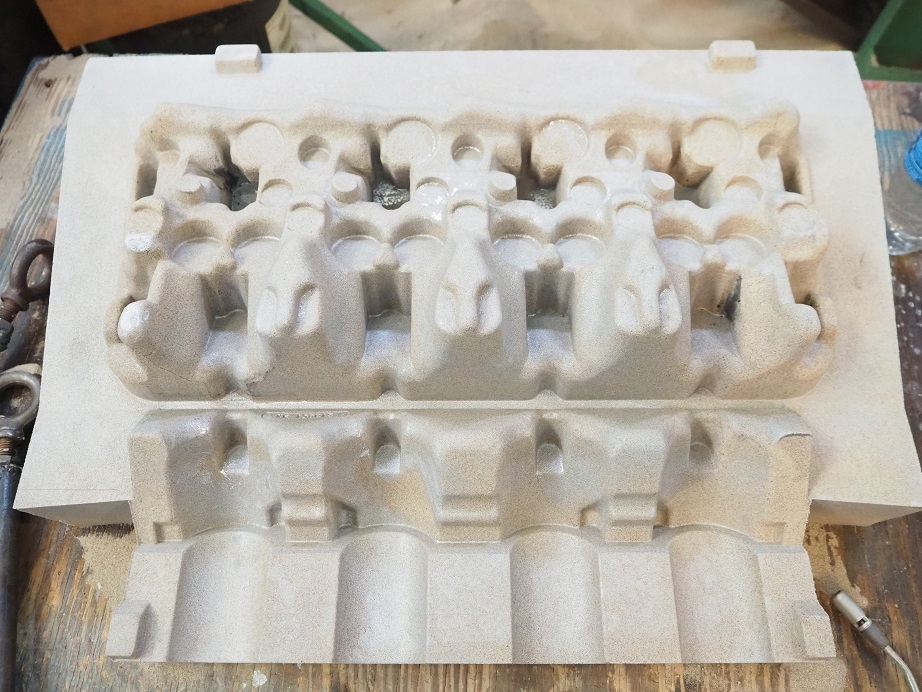
Then the cope, which is the top of the mold, is installed and the mold is ready for pouring. Unfortunately, we ran into a problem with the Ford tooling when it came to the water jacket core. This is a very complex set of three cores, with sand thicknesses down to around 0.100". The foundry guys had trouble getting the sand packed into these molds by hand; our guess is that Ford had a machine to do that, which the foundry doesn't have. Also, even if the mold got completely filled, there was difficulty getting the cores out of the molds without breaking them. Pictures of the core box for the lower water jacket core is below, the second one showing the sand after the box was split back apart after filling. In the second picture we are using glue to hold the sand core together after it broke coming out of the mold.

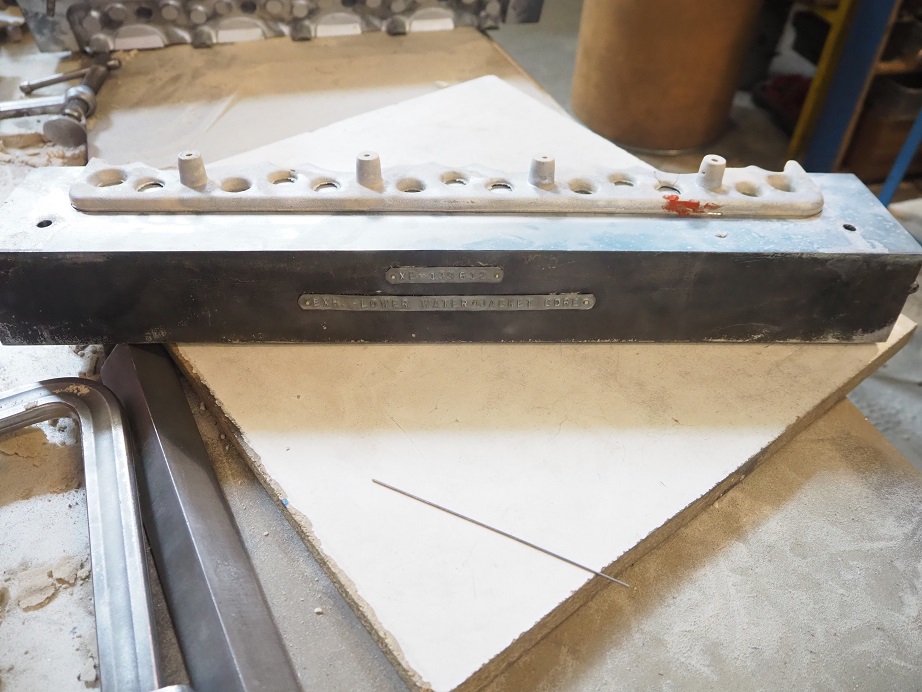
There are three water jacket cores like this, that need to be glued together and then set into the mold. After spending hours just trying to get a good one, I suggested that we go to a 3D printed version, and make it a single core. We are lucky that Dan has the masters for these cores (the masters are what the 3 finished cores are supposed to look like). Dan is going to get them 3D scanned so that we have a file showing what the completed water jacket core is supposed to look like, and then we can get them printed in sand so that we don't have to fight with getting decent cores out of the Ford tooling.
Due to the issues with the water jacket we didn't get to pour a head yet. Hopefully in a month we will be back at the foundry with water jacket cores so we can get some of these poured. Of course, getting good castings is just the beginning of the work. Next they need to be machined, which means machining fixtures will have to be made, and there will be some guessing on the where all the surfaces and holes need to be, because we don't have blueprints for the engine. However, Dan has arranged with the Ford museum to be there and get a detailed look at the engine that they do have, so hopefully that will point us in the right direction.
The block is also going to be an issue, because a standard 429/460 block is nowhere near close to working. The Calliope engine used Cooper rings for sealing the head to the block, and has no provision for water passages from the block to the head; instead, the water from the dual water pumps flows through the block to the back, makes a U-turn into the head at the back via an external fitting, and flows out of the front of the head. Also, the head bolt locations are completely different; there are actually 8 bolts around each cylinder on the Calliope engine, and none of them are in the normal head bolt position in the block. On top of all that, Dan is missing some tooling for the block, and we will have to go to a different foundry for the block because the foundry we are using can't pour a part as large as an engine block. So, basically this is the beginning of a fairly long project, but Dan is committed to getting it done. For my part, I just want to see one of these things running on the dyno ;-)
I will post updates on this project as they happen - Jay