Hi Leny- We know something has to be done with the front shackles. Doing a shackle swap like you're suggesting makes sense too. They're some worn out puppies.
We reached a good stopping point last weekend and could use some advice. We mated the 504 to the C6 and dropped it between the frame rails so we can get to work on mounts before we strip it all down for sandblasting. We know keeping engine/trans close to the rear axle helps with traction. Traction is king in most motorsports, right?

As it sits right now we're against the fire wall. But we think we want to be back another 3 inches or so. This would mean a lot of whittling and fabrication on the fire wall. But is another 3 inches going to really be worth all the work?
We also put the stock steering column back in to see how close it would be to the headers. Not too bad at this point. Another 3 inches back would be doable with some creative tube fab. Better than we thought originally.
What do you guys think?
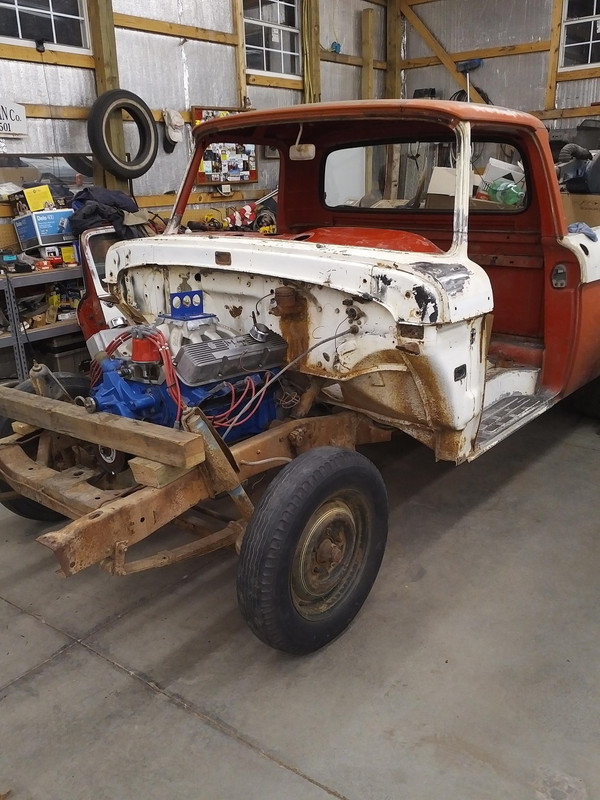